GEDA in the eye of the hurricane
Since 2012 Port Arthur in Texas has been home to the world's biggest steam cracker. The multimillion production site is a joint venture between BASF and ATOFINA and is located in the high-risk hurricane area in the Gulf of Mexico.
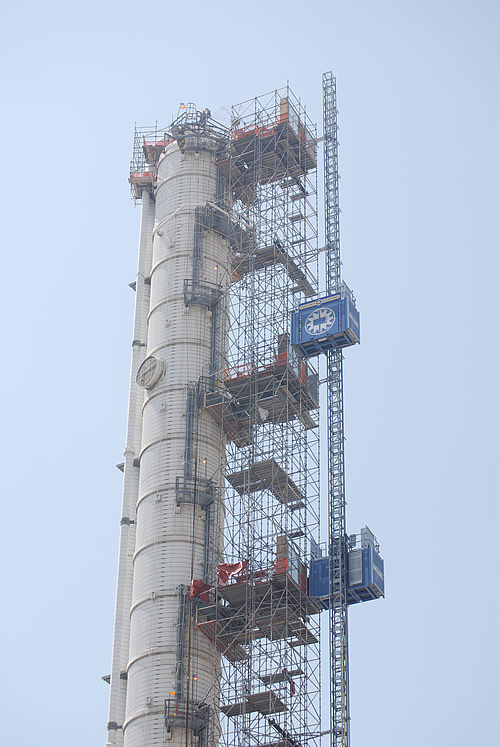
In 1998 BASF and ATOFINA took a decision to build a steam cracker on the site of the ATOFINA oil refinery. Furnaces heat crude oil and break it down into basic chemicals used later to make adhesives, varnishes and polystyrene. The production site is acknowledged as the biggest in the world and has been operational since April/May 2012.
One part of the transformation process takes place in a tower almost 92 metres high. In order to carry out maintenance work simultaneously on all six landings of the tower, staff and material require 24/7 access to the different levels.
Scaffolding was the first pre-requisite here so that sufficient space could be provided for working platforms outside of the tower for arriving and departing materials. The Houston-based scaffolding company BETCO had the challenge of developing a specific anchoring system so that the scaffolding could be fastened to the steel frame of the tower.
But how under these conditions could staff and materials be transported quickly and effectively to the top?
One possibility would have been to use a crane to transport the materials. In that case workers would have had to climb ladders fixed directly on the scaffolding up to a height of 92 metres – a very dangerous alternative!
Therefore BASF commissioned the Houston firm Century Elevators to provide a construction hoist. Century Elevators have been working closely together for many years with the German construction hoist company GEDA-Dechentreiter GmbH & Co.KG and immediately identified that the device to be installed on the Steam Cracker in Port Arthur was the GEDA PH 3240 650 Twin. The benefits of this construction hoist are clear to see. The lift has a lifting speed of 65 m/min with a maximum lifting height of 400 metres. A total of up to 30 people or an overall material weight of 3,200 kg can be transported on the 1.55 x 4.00 metre platform. A PH double car is used on the BASF steam cracker. This means that two cars – one on the left and one on the right side of the mast – can travel upwards and downwards independently of each other.
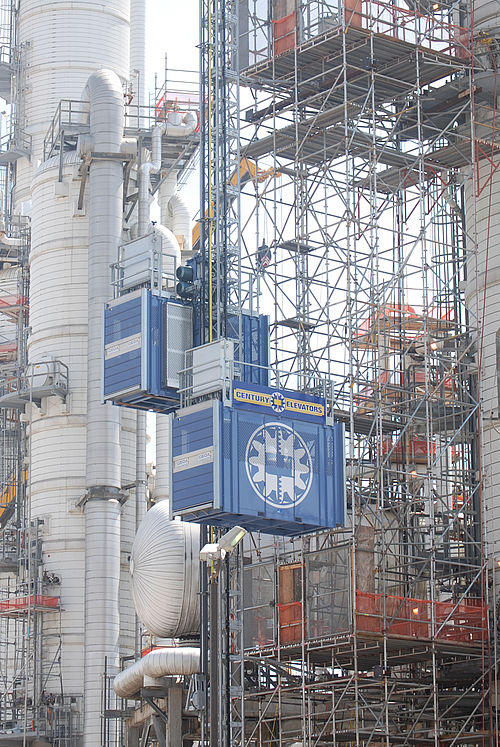
The scaffolding and lift must be attuned to each other with great precision and therefore the scaffolding was specifically strengthened in order to withstand the anchoring forces of the lift with its two cars.
Although most of the maintenance work is to be completed before the start of the hurricane season, the scaffolding and lift mast have been designed to resist hurricane-style wind gusts since the Gulf of Mexico is one of the world's most hurricane-affected regions. The PH 3240 650 Twin is also equipped with a special wind gauge.
GEDA offers an excellent on-site service through its worldwide dealer network. Therefore any issues of adaptations to national rules and regulations can easily be resolved.
Naturally, safety has been the prime focus from the very outset. Before every shift the car, mast and anchorage are inspected and approved for use. Racks, pinions, gates, doors, limit switches, brakes and other electrical and mechanical components are also checked to ensure the safe and precise operation of the lift. Two machine operators and two technicians are on-site 24/7 for the duration of the work.
On the lift itself the well-known safety features including the speed-dependent GEDA safety gear and overload protection, plus limit switches at the top and bottom landings, form part of the standard package.
Despite the hurricane risk the GEDA PH 3240 650 Twin will provide the effective and above all safe transportation of people and materials at the world's biggest steam cracker in Port Arthur until maintenance work is completed.